- UT Policies on Safety and Health
- General Safety
- Safety Suggestions and Hazard Reporting
- Office Safety
- Safety and Health Inspections
- Motor Vehicle Safety
- Fire/Life Safety
- Electrical Safety
- Shop Safety
- Personal Protective Equipment and Respiratory Protection Program
- Confined Spaces
The following sections provide general guidelines and requirements for using personal protective equipment. This chapter covers the following topics:
Definitions
Personal Protective Equipment (PPE) includes all clothing and work accessories designed to protect employees from work place hazards. Protective equipment should not replace engineering, administrative, or procedural controls for safety—it should be used in conjunction with these controls. Employees must wear protective equipment as required and when instructed by a supervisor.It is the responsibility of the Supervisor to ensure their employees are not under protected or over protected. It is also the supervisor’s responsibility to ensure the level of proper protection is documented. This can be done using a PPE Certification Form available from the Safety Office or any other OSHA-compliant PPE certification form.IMPORTANT: Always remove protective clothing before leaving the work area. Do not wear Personal Protective Equipment (PPE) in public elevators, classrooms, restrooms, break rooms, etc.
Arm and Hand Protection
Arms and hands are vulnerable to cuts, burns, bruises, electrical shock, chemical spills, and amputation. Gloves provide protection for the hands and arms from chemicals, temperature extremes, and abrasion. Their proper selection is vital to their ability to protect. This is especially true when dealing with potential exposure to chemicals. It is imperative to remember that both the thickness and the type of material the glove is manufactured from affect the ability to serve as a barrier against a chemical. Specifications regarding compatibility of gloves materials with chemicals is available from the Safety Office.Another factor in the selection of gloves is the wearer’s need for dexterity. It is often advisable to reduce the size and thickness of the glove to increase the dexterity. Caution is also required when using gloves around moving equipment. Gloves should not be used by anyone whose hands are exposed to moving parts in which their hands could get caught.The following is a general list of the types of gloves available:
- disposable latex gloves
- chemical resistant gloves
- leather gloves
- non-asbestos heat-resistant gloves
- metal-mesh gloves for operations cutters
- cotton gloves.
NOTE: Latex gloves are not chemical resistant.Always wear the appropriate hand and arm protection. Double your hand protection by wearing multiple gloves when necessary (e.g., two pairs of disposable gloves for work involving biological hazards). For arm protection, wear a long-sleeved shirt, a laboratory coat, chemical-resistant sleeves or gauntlet-length gloves.Follow these guidelines to ensure arm and hand safety:
- Inspect and test new gloves for defects.
- Always wash your hands before and after using gloves. Wash chemical-protective gloves with soap and water before removing them.
- Do not wear gloves near moving machinery.
- Do not wear gloves with metal parts near electrical equipment.
IMPORTANT: Gloves are easily contaminated. Avoid touching surfaces such as telephones, door knobs, etc. when wearing gloves.
Body Protection
Hazards that threaten the torso tend to threaten the entire body. A variety of protective clothing, including laboratory coats, long pants, rubber aprons, coveralls, and disposable body suits are available for specific work conditions.
- Laboratory coats, coveralls, aprons, and disposable body suits protect employees and everyday clothing from contamination.
- Welding aprons provide protection from sparks.
Never take home contaminated clothing. It can be laundered on campus. Launder reusable protective clothing separate from other clothing.
Hearing Protection
If you work in a high noise area, wear hearing protection. Most hearing protection devices have an assigned rating that indicates the amount of protection provided. Depending on your level of exposure, you may choose from the following devices:
- disposable earplugs
- reusable earplugs
- sealed earmuffs
Earplugs may be better in hot, humid, or confined work areas. They may also be better for employees who wear other PPE, such as safety glasses or hats. Earmuffs, on the other hand, may be better for employees who move in and out of noisy areas, because the muffs are easier to remove. Before resorting to hearing protection, attempt to control noise levels through engineering or operational changes.To avoid contamination, follow these guidelines when using earplugs:
- Wash your hands before inserting earplugs
- Replace disposable earplugs after each use.
- Clean reusable earplugs after each use.
Contact the Safety Office to have your specific area evaluated for hearing protection needs or for more information.
Eye and Face Protection
Employees must wear protection if hazards exist that could cause eye or face injury. Eye and face protection should be used in conjunction with equipment guards, engineering controls and safe practices.
NOTE: Safety glasses or goggles are required in laboratories.
Always wear adequate eye and face protection when performing tasks such as grinding, buffing, welding, chipping, cutting, or pouring chemicals. Safety glasses with side shields provide protection against impact and splashes, but safety goggles provide protection against impact, splashes and hazardous atmospheres. All safety glasses must be ANSI Z87 certified.
Safety Glasses: If you wear prescription glasses, wear goggles or other safety protection over the glasses. Safety glasses with side shields provide primary protection to eyes and are four times as resistant as prescription glasses to impact injuries.
Goggles: Goggles protect against impacts, sparks, chemical splashes, dust, and irritating mist. Wear full goggles, not just safety glasses, when working with chemicals.
Welding: Eyecup welding goggles with filter lenses give protection from glare and sparks. A welding helmet protects from flash burn due to welding, soldering, or brazing, but does not provide primary eye protection; safety glasses or goggles should be worn with the helmet.
Face Shields: A face shield is designed to protect the face from some splashes or projectiles, but does not eliminate exposure to vapors. A face shield should be worn with goggles or safety glasses. See Section 17 (Shop Safety) for more information.
Sunglasses are useful to prevent eyestrain from glare and to minimize ultraviolet light exposure.
Foot Protection
To protect feet and legs from falling objects, moving machinery, sharp objects, hot materials, chemicals or slippery surfaces, employees should wear closed-toed shoes, boots, footguards, leggings or safety shoes, as appropriate. Safety shoes are designed to protect from the most common causes of foot injuries—impact, compression and puncture. Special foot protection is also available for protection against static electricity, sparks, live electricity, corrosive materials, and slipping.
NOTE: Foot protection is particularly important in laboratory, agricultural and construction work.
IMPORTANT: Do not wear sandals or open-toed shoes in laboratories, shops or other potentially hazardous areas. Sturdy leather shoes are appropriate in laboratories.
Head Protection
Accidents that cause head injuries are difficult to anticipate or control. If hazards exist that could cause head injury, employees should try to eliminate the hazards, but they should also wear head protection.
Safety hats protect the head from impact, penetration, and electrical shock. Head protection is necessary if you work where there is a risk of injury from moving, falling, or flying objects or if you work near high-voltage equipment.
Contact the Safety Office for more information.
Safety Showers
Emergency safety showers provide emergency treatment for people exposed to harmful materials. If a person is contaminated with harmful chemicals, the emergency shower provides an instant deluge to protect the person from further exposure. UTIA uses ANSI standards for shower locations, travel distance, testing and function.
- Emergency showers must be located to ensure accessibility within 10 seconds.
- Travel distance between a shower and potential hazards may not exceed 100 feet.
IMPORTANT: Emergency showers are for emergencies only. If a chemical spill occurs involving personal exposure, pull the cord and remove affected clothing immediately. Stay in the shower for at least 15 minutes. Showers are tested annually by the Physical Plant.
RESPIRATORY PROTECTION PROGRAM
The following sections provide respiratory protection guidelines and procedures. This chapter covers the following topics:
Program Overview
This program defines UTIA procedures regarding the use of respirators for personal protection against airborne contaminants. It applies to UTIA employees and to people working for UT as volunteers. The ability of a respirator to provide adequate protection is based on proper selection, fit and training. Respirators which are intended for protection against harmful dusts, fumes, mists, gases, smokes, or vapors must not be obtained or worn by employees without approval from the UTIA Safety Office and in accordance with this program.
This program has been established to comply with the Occupational Safety and Health Act (OSHA) Respiratory Protection Standard, §29CFR1910.134 . The program shall be updated as necessary to reflect changes in workplace conditions that affect respirator use.
Off campus locations may modify this procedure to fit their operations after consultation with the UTIA Safety Office. This may be particularly appropriate for the Research and Education Centers using respiratory protection for pesticide applications, because the OSHA §29CFR1910.134 Respiratory Protection standard does not directly apply to agricultural operations. The requirements of the EPA Worker Protection Standard (§40CFR170) and the OSHA Safety and Health Standards for Agriculture (§29CFR1928) are not reflected in this document. For questions related to these regulations contact the UTIA Safety Office.
This program covers use of air-purifying respirators including: N95 filtering facepiece, cartridge, canister, quarter-mask, half-mask, full-faced, and powered air-purifying respirators (PAPRs). This program does not cover supplied air respirators such as self-contained breathing apparatus (SCBA), air-line respirators, or emergency and escape respirators. For specific requirements regarding these respirators, consult the UTIA Safety Office.
WARNING: Air-purifying respirators do not provide protection in oxygen-deficient atmospheres (less than 19.5% oxygen). If you are unsure if a space or location contains adequate oxygen, the oxygen concentration must be tested prior to anyone entering the space.
Selection of Respirators
Respirator usage has significant limitations. The limitations include difficulty understanding and correctly following usage requirements, poor storage resulting in contaminants on the inside of the facepiece, that the respirator is hot and uncomfortable to wear, that it places a physiological burden on the employee, and that it interferes with visibility. Therefore, other control options (such as product substitution, using wet methods to prevent airborne contaminants, or local exhaust ventilation) are the preferred approach to avoid exposure to harmful air contaminants whenever feasible.
When other control options are not feasible or they have failed to adequately control the airborne hazard, a respirator shall be used by each exposed employee. The proper selection of the respirator and cartridge is critical. If the filter type is not appropriate for the hazard, it will not protect from harmful air contaminants. The useful life of each respirator or cartridge will vary depending on the job duties and actual time in use. To select which respirator is best suited for your operation, contact the UTIA Safety Office.
Only respirators approved by NIOSH (National Institute of Occupational Safety and Health) will be used. Respirators may not be altered and parts (including filters) are not interchangeable between products from different manufacturers.
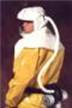
For many UTIA applications the use of Powered Air Purifying Respirator (PAPR) is recommended. A PAPR with a hooded or loose-fitting facepiece places minimal restriction on breathing and provides a higher level of protection. Also, a PAPR with a loose-fitting facepiece doesn’t require fit-testing, and is acceptable for employees with beards or glasses.
Special Provisions for Voluntary Use of N95 Respirators
An N95 filtering facepiece respirator looks similar to a dust mask, but it is made of better filter media and has been tested by NIOSH to provide much better protection against particulate hazards. An N95 respirator will have two straps for a better fit, and the box will have the words “N95” and “NIOSH” on it.
N95 filtering facepiece respirator examples:
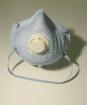
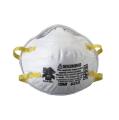
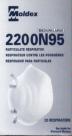
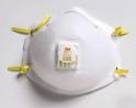
Dust masks that are NOT N95 respirators:

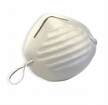
Because these N95 respirators place less physiological burden on the employee than traditional cartridge respirators, no medical approval or fit-testing is required if the usage is voluntary and if you meet the requirements below. However, all voluntary respirator users must read the mandatory OSHA guidance in section 19.13, “Instructions for Voluntary Filtering Facepiece Respirator Use.” This section should be posted next to the storage location for N95 respirators. The following conditions must exist in order for N95 respirators to be used voluntarily:
- Exposure to airborne contaminants is below OSHA permissible exposure limits.
- Exposure is only to non-toxic nuisance materials (plant dust, agar dust).
- There is no exposure to airborne infectious disease agents.
- The N95 respirator is not worn to reduce exposure to gases or vapors.
Program Requirements Summary
UTIA has three primary classes of respirator users, with the requirements for each summarized in the following table. These requirements are described in detail in the following sections.
Responsibilities
UTIA Safety Office Responsibilities
- Serve as the overall program administrator for the UTIA Respiratory Protection Program.
- Develop a written control plan and perform a periodic review to determine if revisions are necessary.
- Provide guidance and technical assistance to departments in the design and selection of appropriate engineering and administrative controls which will reduce the need for the use of respirators.
- Conduct exposure assessments of workplaces to determine the need for respiratory protection.
- Recommend appropriate respiratory protective equipment and cartridge change schedules.
- Conduct fit tests for respirator wearers.
- Provide training on the proper use, care, and storage of respirators. Maintain training records
Supervisors of Employees Wearing Respirators Responsibilities
- Coordinate with Safety Officer on appropriate respiratory protection for employees with airborne exposures.
- Purchase NIOSH approved respirators.
- Initiate medical evaluation process for employees who use respirators (obtain OSHA Respirator Medical Evaluation Questionnaire from Safety Officer).
- Arrange for annual fit testing through UTIA Safety Office. NOTE: loose-fitting PAPR users and voluntary use of N95 are exempt from this requirement.
- Maintain adequate stock of appropriate respirators, cartridges and spare parts.
- Evaluate the effectiveness of the respiratory protection program to ensure that:
- Respirators are properly selected and used
- Wearers receive annual training and fit testing
- Respirators are properly cleaned, maintained and stored
Employee Responsibilities
- Participate in training programs on respiratory protection.
- Read and follow the manufacturer’s information on proper use, cleaning and storage of the respirator.
- Report to the University administration, through their immediate supervisor, any problems that are observed which could compromise health and safety.
- Keep the respirator stored in a protective covering when it is not in use (such as a closed Ziploc bag). Do not leave your respirator sitting out where dust and contaminants accumulate on the facepiece, as these contaminants can interfere with proper faceseal, deteriorate the material, clog the filters, impair visibility, and increase user exposure when the respirator is used the next time.
Medical Evaluation
Respirators place an extra burden on the user because they make it more difficult to breathe, they are hot, and they interfere with normal body movement. Every employee that is required to wear a respirator on the job shall have respirator training and a medical evaluation prior to initial use. Medical approval to wear respiratory protection is the first step in this process. Contact the UTIA Safety Office to obtain a medical questionnaire form. The employee completes the questionnaire and returns it directly to the Occupational Health Nurse (OHN), Mrs. Amy Knowles (336 Ellington Plant Science Building, 2431 Joe Johnson Dr., Knoxville, TN 37996-4564), where it will be reviewed. Employees who indicate potential medical problems on the medical questionnaire will be referred to a physician for medical evaluation. If an employee has questions related to the questionnaire, the OHN will be available to answer them. After review, the UTIA Safety Office is notified in writing of the employee’s physical ability to wear a respirator. Off campus sites can use this process, or other avenues of medical review that are equivalent. There is no charge for the OSHA Medical Questionnaire review, however if additional medical follow-up is required the department is responsible for those expenses. After the initial medical approval to wear a respirator, it is important to realize that a person’s ability to safely wear a respirator can change. Periodic medical re-evaluation is necessary in any of the following circumstances:
- An employee reports medical signs or symptoms that are related to ability to use a respirator;
- Supervisory, safety or medical personnel request re-evaluation;
- A change occurs in workplace conditions (e.g., physical work effort, protective clothing, temperature) that may result in a substantial increase in the physiological burden placed on an employee;
- Information from the respiratory protection program, including observations made during fit testing and program evaluation, indicates a need for employee reevaluation.
Training of Employees
Each respirator user will be trained on how to use, check, and maintain respirators. This training will be provided by the UTIA Safety Office or by a training program that is approved by the UTIA Safety Office. The training of each respirator wearer will include the following:
- The nature, extent, and effects of respiratory hazards to which the person may be exposed.
- Reasons for selecting a particular type of respirator.
- Procedures and schedules for cleaning, disinfecting, storing, inspecting, repairing, discarding, and otherwise maintaining respirators
- An explanation of the operation, capabilities and limitations of the respirator selected.
- Training in the proper use of respirators, including putting on and removing them, any limitations on their use, and their maintenance.
- Instructions as needed for special respirator use.
- Regulations concerning respirator use.
A record will be kept of those employees who have been trained. Each user must understand and be able to apply the contents of this respirator program in the daily use, care, and safekeeping of the respirators.
Respirator Fit Testing
Proper fitting of respirators is essential for employees to receive the protection for which the respirator is designed. Air that passes around the edge of the respirator, rather than through the filter media, is not filtered air. Fit testing will be conducted by the UTIA Safety Office (or other organization with UTIA Safety Office approval), for each employee wearing a tight-fitting type of respirator. The fit-test must be conducted prior to initial use of the respirator, whenever a different respirator facepiece (size, style, model or make) is used, and at least annually thereafter.
- Employees are disqualified from using a tight-fitting respirator (mask forms a tight seal around face) if temple pieces on glasses or facial hair will interfere with the respirator seal (e.g. facial hair on the jawbone, including a day’s growth of stubble). A Powered Air Purifying Respirator (PAPR) with a hood is an alternate option if respiratory protection is required.
Tight-fitting respirators should not be worn if scars, hollow temples, excessively protruding cheekbones, deep creases in facial skin, the absence of teeth or dentures, or unusual facial configurations prevent a good face seal.
Maintenance of Respirators
One of the best indicators of a successful respiratory protection program is the proper care, maintenance and storage of respirators. Respirators shall be cleaned and disinfected as necessary. Always follow the manufacturer’s recommendations regarding cleaning and disinfection. Respirators shall be inspected by the employee before each use for damaged or missing parts. Parts, including cartridges, are not interchangeable between respirators from different manufacturers.
- Each respirator shall be stored in a plastic bag.
- Respirators shall not be stored in areas where they will be subject to high heat, chemicals, physical damage, extreme cold or theft.
Program Evaluation
Periodic evaluation of the effectiveness of the respirator program is essential to ensure that persons are being provided with adequate respiratory protection. The effectiveness of the respirator program should be evaluated at least annually by supervisors and the UTIA Safety Officer. Corrective action should be taken to correct defects found in the program. Supervisors will monitor the effectiveness of this program by:
- Frequent unscheduled observations of employee activities throughout the work area to confirm proper respirator use and acceptance by employees.
- Observation of and discussion with new employees to confirm proper training has been carried out.
References
OSHA Respiratory Protection Standard (§29 CFR 1910.134)OSHA Occupational Safety and Health Standards for Agricultural (§29 CFR 1928)EPA Worker Protection Standard (§30 CFR 170)Industrial Respiratory Protection (NIOSH Publication)Respirator Decision Logic (NIOSH Publication)Review Date – July, 2006
OSHA Handout – Instructions for Voluntary Use of Filtering Facepiece Respirators
Excerpted from OSHA 29 CFR 1910.134 Appendix D, Information for Employees Using Respirators When Not Required Under the Standard
Respirators are an effective method of protection against designated hazards when properly selected and worn. Respirator use is encouraged, even when exposures are below the exposure limit, to provide an additional level of comfort and protection for workers. However, if a respirator is used improperly or not kept clean, the respirator itself can become a hazard to the worker. Sometimes, workers may wear respirators to avoid exposures to hazards, even if the amount of hazardous substance does not exceed the limits set by OSHA standards. If your employer provides respirators for your voluntary use, or if you provide your own respirator, you need to take certain precautions to be sure that the respirator itself does not present a hazard.
You should do the following:
- Read and heed all instructions provided by the manufacturer on use, maintenance, cleaning and care, and warnings regarding the respirators limitations.
- Choose respirators certified for use to protect against the contaminant of concern. NIOSH, the National Institute for Occupational Safety and Health of the U.S. Department of Health and Human Services, certifies respirators. A label or statement of certification should appear on the respirator or respirator packaging. It will tell you what the respirator is designed for and how much it will protect you.
- Do not wear your respirator into atmospheres containing contaminants for which your respirator is not designed to protect against. For example, a respirator designed to filter dust particles will not protect you against gases, vapors, or very small solid particles of fumes or smoke.
- Keep track of your respirator so that you do not mistakenly use someone else’s respirator.